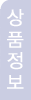 | |
Model CP20 SLA - New Product!
 |
On-line Sonic Liquid Analyzers. The CP-20 SLA (Sonic Liquid Analyzer) is used to measure the strength, amount or concentration of acids, bases, salt solutions, emulsions, oils in water, alcohols, sugar solutions, non-aqueous liquid mixtures, polymers, and many others. The only absolute requirement is that the liquid be acoustically transparent.
|
¡¡
- Concentration, Dissolved Solids, Wt. %, Vol %, Density, ¡ÆBrix.
- In-Line Sensor Provides Real Time Analysis.
- No Scheduled Maintenance Requirements!
- Extreme Calibration Stability, Guaranteed for 3 Years!
- Typical Accuracy Better Than 0.10 Weight %!
- Factory Calibrated for Easy Installation and Start-up!
- Industry Standard Dual 4-20 Outputs and Alarms.
- Robust NEMA 7 Enclosure With Display.
- Automatic Temperature Compensation.
- Internal 8000 Point Data Logger.
- All Welded, Seal-less Sensors Available.
- Easy Re-configuration and Powerful Diagnostics via Laptop/PC.
For more detailed information see the following:
-
Selecting an Inferential AnalyzerThe Model CP20 can often be used with great benefits in applications historically reserved for other inferential process analyzer technologies such as conductivity meters, densitometers, or refractometers. A conductivity meter is used inferentially when a conductivity of 126 mS is observed for a liquid known to consist of common salt, and is at a temperature of 20 ¡Æ C and therefore a salt concentration of 10 percent by weight is inferred because 126 mS is the published value for 10 Wt. % common salt. Similarly, we have NuSonics Div. has a database of values of sound velocity for hundreds of chemicals and liquids which is used to calibrate the CP20 to provide the analysis value.
Inferential analyzers work best either in binary liquids or in liquids in which only one ingredient is changing.
¡¡
-
Sensor Mounting and Materials
 |
An assortment of sensors are available for use with the CP20. These include tri-clover or flange mount insertion sensors, inline spool pieces or filler flange wafer sensors, and low volume small line flow through sensors. These sensors are available in a variety of materials including 316 or 304L stainless steel, Hastelloy B, C, Alloy 20, PVDF (Kynar), and polypropylene. Certain sensors are suitable for CIP or no-metal-contact processes. Options are available for sensors operational to 350 ¡Æ C (660 ¡Æ F), 2000 PSIG, and the harshest of chemical environments. The Model CP20 is preferably attached directly to the sensor, but may be separated from the sensor by use of interconnecting cables installed in conduit. In most cases, the CP20 can be used with existing NuSonics sensors. | ¡¡
-
What's New in the Model CP20The Model CP20 takes advantage of the recent development of low cost, high speed digital signal processors. Previous versions of Sonic Liquid Analyzers transmitted a single pulse of sound, and a timing circuit measured its transit time. The frequency of the transmitted sound was determined by the physical dimensions of the transmitting acoustic crystal. The model CP20 uses a novel continuous pulse approach. The transmitting crystal is excited by a sine wave signal, and the received sine wave is digitized. The excitation sine wave frequency can be easily varied. Continuous excitation of the crystal results in higher decibel levels transmitted. By automatically varying the frequency, chemicals or liquids which absorb sound at some specific frequency or processes can now be successfully measured.
The Model CP20 also takes advantage of the common availability of laptop and personal computers. These devices can function as a high quality user-friendly interface utilizing a powerful factory provided software package. The software contains easy to use procedures for checking the calibration and printing reports to meet the documentation needs of many certification programs. The Model CP20 also incorporates an 8000 point data logger. The software allows many forms of manipulating this data, from graphing it to using it for calibration adjustment or new application setup. |
¡¡
Application Notes:
Specifications:
Operational |
Display |
2 Line by 16 Character |
Power |
24 VDC, 115 VAC, 230 VAC, 24 VAC Options |
Analog Outputs |
Dual 4 — 20 mA Outputs |
Digital I/O |
RS-232 & RS 485 |
Relays |
Three SPDT relays, .1A @ 115VAC, intended for PLC or DCS interface (High, Low and Fault) |
Ambient Temp. |
-20 to 70 ¡Æ C (-5 to 160 ¡Æ F) |
Mechanical |
Enclosure |
NEMA 7 Explosion Proof & Water Resistant with window (meets Class 1, Div.2 groups B, C, D and others) |
Weight |
Varies with sensor style selection, typically less than 25 lbs. |
Mounting |
Standard: 2" 150# ANSI flange. Other sizes and configurations available |
Wetted Materials |
Standard: 316 Stainless Steel, also available in 304 SS, C20, Hastelloy B & C, Polypropylene, Kynar (PVDF) and other materials. |
Performance |
Range |
Sound Velocity: 500 - 3000 meters/sec (any acoustically transparent liquid) Temperature: -15 to 185 ¡Æ C (5 — 365 ¡Æ F) Standard |
Resolution |
Sound Velocity: ¡¾ 0.01 meters/sec Temperature: ¡¾ 0.01 ¡Æ C |
Repeatability |
Sound Velocity: ¡¾ 0.10 meter/sec Temperature: ¡¾ 0.05 ¡Æ C |
Response Time |
2 Seconds |
Accuracy |
Sound Velocity: ¡¾ 0.20 meter/sec Temperature: ¡¾ 0.10 ¡Æ C Concentration: Application Dependent, typical values are ...
Acids and Caustics: ¡¾ 0.05 Wt. % Salts: ¡¾ 0.1 Wt. % Organic liquids: ¡¾ 0.1 to 0.2 Wt. % Oils in water: ¡¾ 0.2 Vol. % Sugars: ¡¾ 0.1 ¡ÆBrix |
Calibration Stability |
3+ Years, based on 0.003 mils/year corrosion rate of wetted materials. |
Certifications |
N.I.S.T. traceable certificates available for certain applications. |
Setup |
Factory default, RS232 digital link to PC or laptop. |
Software |
Requires Windows 95, NT or better, 8 Mb RAM preferable. |
 |
Note: Specifications are subject to change without notice. | |
BINARY AQUEOUS SOLUTIONS AND SLURRIES |
Acetaldehyde Acetic acid Acetic anhydride Acetone Activated carbon slurry Acrylonitrile butadiene copolymer Adipic acid Alkanolamine oleate Alum Alumina fines Alumina hydrate slurry Aluminum chlorhydrate Aluminumsulfate Amines Ammonia Ammonium bisulfite Ammonium carbonate Ammonium chloride Ammonium hydroxide Ammonium molybdenate Ammonium nitrate Ammonium persulfate Ammonium sulfate Bauxite slurry Bayer liquor (aluminumprod.) Bismuth octoate Black liquor Boric acid in Sodium sulfate solution Boric acid Brine Butadiene rubberslurry Butanol Calcium carbonate Calcium chloride Calcium hydroxide Calcium nitrate | |
Calcium sulfate Caprolactam Chlorine dioxide Chlorine salts Citric acid Clay slurries Cleaning concentrates Cobalt acetate Coolant oil emulsions Copolymer latices Copper sulfate Corn starch Cupric chloride Cupriethylene diamine Cyanides Defoamers Detergent solutions Diammonium phosphate Dibutyl phthalate Diethanolamine Dimethyl formamide Emulsified rosin Ethanol Ethylene dichloride Ethylene glycol 2-Ethylhexanoic acid Ferric chloride Ferrous sulfate in Sulfuric acid Finish solutions Flocculant Fluorosulfonic acid Fly ash slurry Formaldehyde Formic acid Glycerin Graphitesolids Gypsum Hexamethylenediamine Hydrochloric acid Hydrofluoric acid | |
Hydrogen peroxide Hydrosulfite Indigo solids in Caustic Ion exchange resins Isophthalic acid Isopropyl alcohol Isopropylamine Latex Lithium bromide Lithium hydroxide Magnesium bisulfite Magnesium sulfate Magnesium sulfite Methanol (Methylalcohol) Methyl deithanolamine Methyl ethyl keytone Methylene chloride Mica slurry n-Methyl pyrrolidone Nitric acid Nylon finishes Nylon salt Oleum Oil / water emulsions Ore-leaching solutions PVCsuspension Paints Paper-coating latices Phenol Phosphate slurry Phosphoric acid Polyglycol / potassium hydroxide Polymer (floor- wax)emulsion Polystyrene Polyvinyl acetate Polyvinyl alcohol Potassium - butylphosphate Potassium carbonate Potassium chloride Potassium hydroxide | |
Potassium permanganate Propanediol Propylene glycol Rayon spin bath liquor Red liquor Rolling Oils Salicylic acid slurry Saline solutions Silver nitrate Sodium bichromate Sodium borate Sodium carbonate Sodium chlorate Sodium chloride Sodium formate Sodium hydroxide Sodium hypochlorite Sodium lauryl sulfate Sodium nitrate Sodium silicate Sodium sulfate Sodium sulfide Sodium thiocyanate Sorbic acid Spent sulfite liquor Styrene butadiene rubber Sulfite liquor Sulfuric acid Surfactants t-Butyl alcohol Taconite slurry Terathane waste acid Terephthalic acid slurry Tetrahydrofuran Thixotropic pigments Titanium oxide Toluene Urea Urea formaldehyde resin Vinyl / butyl acetate | |
TRINARY AQUEOUS SOLUTIONS |
Copper Sulfate / Sulfuric Acid / WaterCupric Chloride / Hydrochloric Acid / Water |
Hydrocarbons / Sulfuric Acid / Water (Alkylation Acid) / Potassium Hydroxide / Potassium / Fluoride / Water |
NON-AQUEOUS SOLUTIONS AND SLURRIES |
Acetic anhydride in Acetic acid Acrylic acid in Monomer Acrylic latexes Acrylic polymer in Toluene / butanol Alkyd resin Ammonia in Nitroaniline Aniline Antimony trioxide slurry in Ethylene glycol Carbon tetrachloride Cellulose acetate in Acetic acid Cellulose acetate in Acetone Cephalosporin in Methylene chloride Cephalothin slurry in Alcohol Coal tar pitch Coal / mineral oil slurry Coke tar Copolymer in Hexane Creosote Cyclohexanone in Cyclohexane Diatomaceous earth in Heptane | |
Diethylhexyl phthalate in Adipate polyester Epoxy polymer in Organic solvent Epoxy resins Ethanol in Caustic Ethylene glycol in Terephthalic acid Ethylene oxide Ethylenediamine in Toluene Film developer Formamine Freon in Oil Homopolymer in Hexane Homopolymer/copolymer in Iso-octane Methanol in Methyl acetate Methyl methacrylate in Ethyl acrylate Modacrylic polymer in Dimethyl formamide NORDEL in Hexane Oleum Organic peroxides | |
Orthene in Methylene chloride p,p-Bisphenol A in Phenol Phenolic resin Polycarbonate in Methylene-chloride Polyester resin in Monomer Polyester resin solids in Styrene Polyethylene Polymers in: Xylene Toluene Alpha-methylstryrene Ethyl acrylate Iso-octane Cyclohexane Polymer solids in Hexane Polymerization rate, M.W. Polyolefin lubricants Polyphenylene oxide in Toluene Polysiloxane rubber Polystyrene in Styrene Polystyrene solids in Polyglycol | |
Polysulfide Polyurethane in Tetrahydrofuran Polyvinyl acetate in Methanol Polyvinyl chloride Resin in Toluene Resin in Toluene / Heptane Rubber in: Methylene chloride Xylene Styrene Saran Silicone oils Silicone polymers Siloxane rubber Soybean oil in Hexane Soybean oil hydrogenation Spin bath liquor Styrene in Ethylbenzene Succinic acid in Succinic anhydride Sulfur chloride in Sulfur dichloride Sulfur Trioxide in Fluosulfonic acid Terephthalic acid | |
FOOD PRODUCTS |
Apple juice / Concentrate Beer (wort plato) Beet sugar Butter Caffeine Catsup Cheese slurry Coffee extract | |
|
Grape juice / Concentrate Ice cream Jelly Liquid protein Margarine oils Milk products Molasses Orange juice | |
Palm oil Pectin Soft drinks Sucrose (dilute) Sucrose syrup Tea extract Vegetable oils Wines | |
PETROLEUM PRODUCTS / INTERFACE DETECTION |
#2 Fuel oil Alkylation acid Asphalt Bunker ¡°C¡± | |
Coal / fuel oil slurry Coal / kerosene slurry Crude oil Diesel fuel | |
Standard Low sulfur Fuel Oils Gasoline | |
Regular Unleaded Premium Jet fuel | | |
¡¡
Sonic Concentration Analyzers determine liquid concentration, density, % solids, weight %, volume %, ¡ÆBrix and others by measuring sound velocity. The sound velocity of any liquid or mixture is a repeatable and measurable physical property. The relationship between sound velocity, liquid composition and temperature is different for every liquid. Once the relationship between sound velocity and the desired variable is known, sound velocity can be used to accurately monitor changes in liquid composition. The results of this measurement are often the only means to obtain real time high accuracy concentration or density output. The precision of our concentration analyzers make them an excellent choice for process and laboratory measurement. |
InstrumentMeasurement of sulfuric acid concentration using the Sonic Concentration Monitor.
IndustriesFertilizers, chemical manufacture, petroleum refining, rayon, sulfuric acid manufacture.
IntroductionThe conversion of sulfur dioxide gas to sulfuric acid has increased in recent years due to the enforcement of stringent anti-pollution laws. The supply increase has resulted in a profit squeeze, meaning that producers of sulfuric acid must incorporate all possible cost reduction techniques into the manufacturing process. The Sonic Concentration Monitor, which uses the velocity of sound as the measured parameter, aids in highly accurate automated manufacturing, greatly reducing production costs by keeping operating points at their optimum values. Savings are illustrated under the heading PAYBACK.
Test Conditions Sulfuric acid is produced chiefly in concentrations of 93% to 98%. Consequently, reagent grade sulfuric acid in concentrations from 77% to 100% by weight have been tested for sound velocity at temperatures between 20¡Æ C and 60¡Æ C and at ambient pressure.
ResultsFigure 1 shows the average intrinsic error of analysis when using the Sonic Concentration Monitor. The error is below ¡¾0.1% acid for concentrations above 80% and below ¡¾0.02% for concentrations above 90%. Figure 2 gives the sound velocity vs. concentration curves at 10¡Æ C intervals. Note that the curves are the same shape with the slope increasing with concentration. Figure 3 is a graph of the temperature coefficient as a function of concentration. The coefficient and reference process temperature are entered as a polynomial into NuSonics' Models 86 or 88 process monitor in order to temperature-correct the concentration reading when the process temperature departs from the reference point.
DiscussionThe intrinsic error of any instrument used to measure concentration is inversely proportional to the slope of the measured variable vs. concentration. The density curve flattens out above 95%, and the conductivity curve flattens below 94%. Consequently the errors of analysis of densitometers and conductivity sensors are large in these respective regions and it is in these regions that the Sonic Concentration Monitor offers greatest benefit. Figure 2 clearly illustrates that the sound velocity curve has a steep slope throughout the range of concentrations provided by industry, resulting in the remarkable accuracies displayed in Figure 1. The Sonic Concentration Monitor is also more accurate than refractometers and not subject to fouling.
Payback As an illustration of cost savings due to accurate analysis, consider a plant which substitutes a NuSonics' monitor for another type sensor, thereby (conservatively) improving analysis by 0.4%. On a daily basis a plant producing 770 tons per day at $28 per ton would save:
0.4% x 770 tons / day x $80 / ton = $246 day At this rate, the plant could easily afford to pay for a monitor within a few months. The increase in profits in subsequent years is obvious dependability mean higher profitability in any plant where the concentration.
ConclusionThe Sonic Concentration Monitor is the most accurate real time output instrument in the 80% to 100% sulfuric acid range. It is the only instrument that can be used over the entire range of commercial concentration with remarkable accuracy. In addition, the Sonic Concentration Monitor has no moving parts and its accuracy is not degraded by fouling as are densitometers, conductivity sensors, and refractometers. Its accuracy and dependability mean higher profitability in any plant where the concentration of H2SO4 must be carefully measured and/or controlled.
¡¡
¡¡
-------------------------------------------------------------
Model 87 Laboratory Analyzer
 |
Model 87 is a lab adaptation widely accepted process composition analyzer, used in both industry and research for over twenty years. Employing acoustic technology, the Model 87 continuously samples the sound velocity and temperature of a liquid and produces a concentration output based on those measurements.
|
- Displays Concentration in a Variety of Units
- Instantaneous Measurement- Faster, Easier, and More Repeatable Than Titration
- Up to 0.02% by Weight Accuracy
- No Moving Parts and Virtually No Maintenance
- Measure Acids, Bases, Organics, Polymers and Many Others
Specifications:
Power Requirements: |
115V AC (+/-10%) or 230V AC (+/- 10%) 50 to 60 Hz |
Power Consumption: |
35 Watts |
Output Signal: |
- Concentration: 4-20 mA into 600 ohms max
- Temperature: 4-20 mA into 600 ohms max
- Attenuation: 0-10V DC into 10000 ohms
- Fault/High/Low Relay: Form C Relay 1.5 A @ 115V AC, 1.0 A @ 230V AC
- Link: RS-232, 50-19, 200 baud
|
Compensation Range: |
0-100¡Æ C (other ranges available to 400¡Æ C) |
Display: |
Liquid Crystal (LCD) 2-Line x 16 character |
Dimensions: |
- Transmitter:
8.2" (20.8 cm) height 8.3" (21.1 cm) width 15.0" (38.1 cm) depth
- Base:
11.5" (29.2 cm) width 16.5" (41.9 cm) depth
- Transmitter and Base:
14.8" (37.6 cm) height 21.8 lbs. (9.9 kg) weight |
TRANSDUCERS |
Operating Temperature: |
-40¡Æto 150¡Æ C (-4¡Æ 0 to 302¡Æ F); option to 400¡Æ C |
Materials: |
316 Stainless Steel (standard), Carpenter 20, Hastelloy B & C, Titanium, Zirconium, KYNAR, high-density polypropylene |
Cable length: |
8 feet (standard) |
Repeatability: |
Typically +/- 0.005 to +/- 0.1 weight percent |
Note: Specifications are subject to change without notice. | | | |
|
|
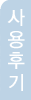 | |
 |
¹øÈ£ |
Á¦¸ñ |
ÀÛ¼ºÀÚ |
ÀÛ¼ºÀÏ |
Æò°¡Á¡¼ö |
|
 |
|
ÀÌ »óǰ¿¡ ´ëÇÑ »ç¿ëÈıⰡ ¾ÆÁ÷ ¾ø½À´Ï´Ù.
»ç¿ëÈı⸦ ÀÛ¼ºÇØ ÁÖ½Ã¸é ´Ù¸¥ ºÐµé²² ¸¹Àº µµ¿òÀÌ µË´Ï´Ù. |
|
 |
|
 |
|
|
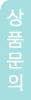 | |
 |
¹øÈ£ |
Á¦¸ñ |
ÀÛ¼ºÀÚ |
ÀÛ¼ºÀÏ |
´äº¯ |
|
 |
|
|
|
 |
|
 |
|
|
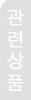 | |
ÀÌ »óǰ°ú °ü·ÃµÈ »óǰÀÌ ¾ø½À´Ï´Ù. | |
|
|